Требования к печатным платам
Если говорить о требованиях, предъявляемых к печатным платам в плане сборочно-монтажного производства, то здесь стоит выделить ряд моментов:
- Размеры изделия. Внимание необходимо обратить как на сам размер контактной площадки, так и на зазоры между ними. Если процесс изготовления печатной платы предлагает использование сборочно-монтажной линии, то к обязательным требованиям относят и габариты групповой заготовки, ее соответствие размерам конвейерной ленты.
- Система базирования. Важны при монтаже многовыводных компонентов на рабочей поверхности. Форма, размер, положение на плате, контактных площадок всегда согласуются между производителями плат и представителями сборочных цехов.
- Выбор химии под пайку. От его типа зависит выбор флюса, типа пасты, рабочий температурный режим. Устойчивость сборочно-монтажного производства зависит от времени сохранения финишного покрытия платы свойств под пайку.
- Коробления платы. Именно деформационные изменения, отклонения от идеально ровной поверхности изделия и приводит в 90% случаев к браковке готового изделия. Минимальное коробление – обязательное условие для установщика компонентов.
- Стойкость платы к высокотемпературным воздействиям. Температурный диапазон, в пределах которого изделие способно сохранять свою форму и свойства определяет применимость тех или иных способов пайки. Нередко сегодня используются материалы с высокой температурой стеклования. По цене они будут выше аналогов, но зато их надежность в процессе пайки без свинца значительно выше.
- Свойства паяльной маски, качество ее нанесения на основу. Важно то, насколько точно теплостойкий защитный материал совмещается с монтажным полем, есть ли он в зазорах между компонентами, нет ли его на контактных площадках. То, какую влажность и температуру паяльная маска способна выдержать, сказывается на стойкости готового изделия к эксплуатационным условиям.
- Наличие и качество маркировки. Она должна быть четкой, хорошо читаемой, нестираемой. Нередко ее применяют при монтаже компонентов для их центрирования. И в этом случае еще важный момент – точность размещения реперных знаков, выполненных в форме маркировки.
- Пригодность платы для диагностики качества. На ее поверхности должны присутствовать дополнительное точки для контакта с зондами. Да, в этом случае несколько снижается плотность размещения компонентов. Но зато тестирование позволяет убедиться в высоком качестве электронного модуля и его пригодности к использованию.
- Точность позиционирования точек на плате, минимальные зазоры между дорожками меди, между элементами маркировки и маски. Минимальная толщина наносимых линий - маски, меди, маркировки.
- Импеданс. Требования к переходным отверстиям. Требования к дополнительным технологическим операциям - если мы говорим о требованиях на этапе производства. Если входной контроль, то: точность габаритных характеристик, выдерживание толщины платы. Отсутствие нарушений маски, читаемость маркировки, доступность не менее 50% от площади контактных площадок под пайку (при смещении растекании маски). Отсутствие серьезных царапин и ударов, влияющих на целостность токопроводящего покрытия.
Только при соблюдении всех этих требований можно говорить о высоком качестве готового изделия и его пригодности к установке в электронику.
Материалы для производства печатных плат
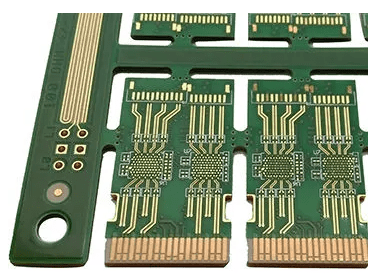
Технология производства печатных плат предполагает использование нескольких категорий материалов:
- Токонепроводящая подложка. Вариантов много: стеклотекстолит, керамические пластины, фторопласт, алюминий, нержавейка, медь, полиамидные пленки. Материал подбирается исходя из технологии изготовления.
- Токопроводящий материал. Это фольга. Она может быть простой медной, гальваностойкой, электроосажденной или отожженной катаной. Также может применяться дополнительно обработанный материал с минимальным уровнем шероховатости или фольга с резисторным подслоем. Наиболее часто применяется продукт толщиной от 12 до 105 мкм.
- Связующий слой. Может применяться адгезив, эпоксидные, акриловые полимеры (препреги). Препреги преимущественно применяют для прессования многослойных изделий.
- Финишное покрытие. Им обрабатываются части пластины, не покрытые паяльными масками. Призвано обеспечить высокое качество пайки. Преимущественно применяют бессвинцовые, оловянно-свинцовые припои, иммерсионное серебрение или золочение, органические составы.
Методы изготовления печатных плат
Сегодня на практике распространено несколько разновидностей технологических процессов изготовления печатных плат. И во многом они зависят от методов производства:
- Комбинированный позитивный.
- Металлизация сквозных отверстий.
- Попарное прессование.
- Субтрактивный.
- Послойного наращивания.
- Аддитивный.
Рассмотрим более подробно каждый из них.
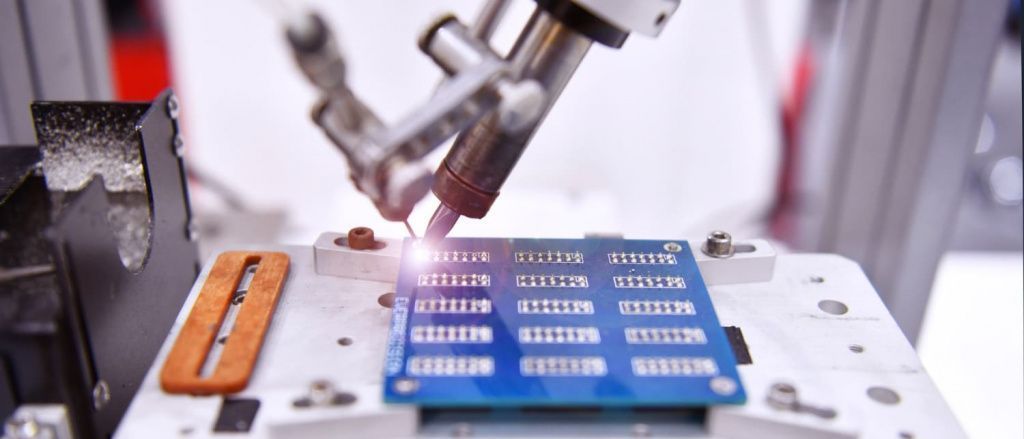
Комбинированный позитивный метод
Относится к полуаддитивным. Применяют при производстве двухслойных и многослойных плат, выполненных методом попарного прессования. Предполагает применение фольгированного токонепроводящего основания. Толщина фольги минимальна – от 5 до 18 мкм. Формирование рисунка идет путем гальванического осаждения меди на основании специальных фотошаблонов.
Комбинированный позитивный метод производства печатных плат имеет следующие преимущества:
- высокая точность печатного рисунка;
- надежная защита диэлектрического основания от технологических растворов;
- высокие адгезионные свойства между основанием и токопроводящим рисунком.
Но здесь есть и недостатки. Так, в результате травления появляется боковой подтрав проводников, что вносит ограничения в разрешающую способность процесса. Если этот метод использовать для производства многослойных плат, то необходимо применять металлорезистор. А это уже усложняет сам процесс (его надо будет удалять после травления), повышает его стоимость.
Металлизация сквозных отверстий
Предполагает производство многослойных плат путем прессования в один пакет отдельных внутренних слоев химическим способом. Только после этого просверливают отверстия и металлизируют их.
К достоинствам метода относят:
- автоматизацию производства;
- простоту технологического процесса;
- минимальную чувствительность к браку, что повышает выход готовой продукции;
- высокую скорость производства;
- хорошую скорость производства рисунка топологии, повторяемость: можно приметь при крупносерийном выпуске товара;
- минимизацию бокового подтрава, что позволяет выпускать высокоточные узкие проводники;
- возможность изготовления плат с любым числом слоев, разных параметров, что позволяет минимизировать такой недостаток, как невысокая плотность размещения компонентов;
- отсутствие переходов между слоями позволяет применять тончайшие основание, не проводящее ток;
- возможность включения в конструкцию экранирующий, питающих слоев и пр.
Из слабых сторон выделяют недостаточно сильную связь торцевых частей контактных площадок и самой металлизации. Повысить качество работ позволит четкое соблюдение отношения минимального диаметра отверстия к общей толщине платы 1:8. Не обойтись и без правильного задания режимов прессовки, соблюдения равномерности полимеризации смолы.
Метод попарного прессования
Предполагает создание межслойных соединений путем металлизации отверстий. Из таких заготовок в последующем формируются многослойные платы. Достоинств у этого метода несколько:
- простота выполнения работ;
- высокая скорость: заготовки производятся в одном технологическом цикле;
- минимальная восприимчивость к браку, что повышает выход товарной продукции.
Но здесь технология предполагает двухкратное осаждение гальванической меди на наружных слоях платы, что ухудшает разрешающую способность электропроводящей дорожки. Также требуется применение специальных материалов для печатной маски и заготовок более высокой жесткости, что ограничивает допустимое число слоев. Все это относится к недостаткам этого метода.
Химический субтрактивный метод
Субтрактивный метод применяется при производстве однослойных плат или внутренних слоев многослойных изделий, выполненных путем металлизации сквозных отверстий и послойного наращивания. На диэлектрик, покрытый фольгой, наносят рисунок с использованием печатных проводников, стойких к растворам травления. Получается, что после травления на поверхности платы остаются только токопроводящие дорожки. Защитная пленка наносится методом трафаретной печати, фотолитографии (применяется фоторезист).
Процесс производства таких плат полностью автоматизирован, что повышает его производительность и снижает себестоимость. Из недостатков метода выделяют достаточно большие подтравы, необходимость применения дорогих фольгированных материалов. При этом большая часть меди на этапе травления будет просто удалена, а полученные растворы надо будет должным образом утилизировать.
Метод послойного наращивания
Предполагает последовательное соединение проводникового и изоляционного слоя. Соединение токопроводящих элементов выполняется в отверстиях изоляции путем гальванического наращивания меди. Метод послойного наращивания обеспечивает высокую плотность размещения электрокомпонентов по всех слоях платы и самого монтажа.
Но допустимое количество слоев здесь ограничено, а необходимость применения меди повышает себестоимость изделий. Весь процесс производства занимает несколько часов, что также относят к недостаткам. При наличии дефекта на одном из слоев, бракуется вся деталь, что снижает выход товарной продукции.
Аддитивный метод
Аддитивный метод получения рисунка печатной платы предполагает нанесение токопроводящей дорожки на нефольгированный материал путем химического меднения через защитную маску. Такое решение обеспечивает высокую надежность соединения компонентов, их однородность (нет подтравливания). При травлении не используется гальваническое покрытие, что исключает необходимость утилизации раствора. На практике этот метод преимущественно применяется при изготовлении многослойных плат с металлизированным отверстиями. Но себестоимость таких изделий будет в 3-4 раза выше, чем у тех, которые получают путем гальванического осаждения.
Технология изготовления печатной платы
На практике, особенно в ремонтных и любительских условиях чаще всего применяют 3 технологии производства печатных плат:
- Способ переноса. Предполагает дополнительное применение временной подложки (как вариант, миллиметровой бумаги). На такой основе закрепляются проводники печатного монтажа из латунной или медной фольги. Все это наносится на диэлектрическое основание, а после подложка удаляется. Основное требование к диэлектрику – достаточно ровная, плоская поверхность. Здесь не нужны дорогие материалы, оснастка.
- Механический способ. На фольгированную диэлектрическую основу (гетинакс) наносится рисунок токопроводящей дорожки. Далее фольгу с пробельных мест удаляют любым механическим способом – фрезой, ножом, скальпелем, резаком. В реализации метод не очень простой, ведь требует от исполнителя высокой точности.
- Химический способ. Очень схож с предыдущим вариантом. Также используется фольгированная подложка. На нее наносится рисунок. Вот только фольга с пробельных мест удаляется путем травления. Преимущественно применяется раствор хлорного железа. Полученная смесь после завершения работ требует утилизации.
Более подробно с каждой технологией изготовления печатной платы можно узнать у специалистов компании «Фрегат».